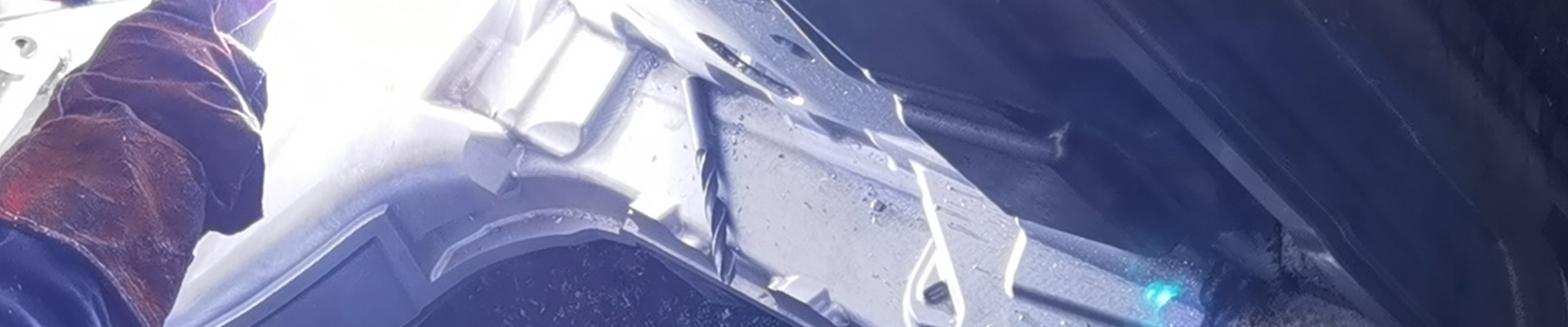
- ブログ -
19
2025
-
03
高精度鋳造部品のCNC加工における画期的な進歩により、製造効率が向上しました
著者:
高度なCNC加工技術が鋳造後の仕上げ工程に革命を起こす中、世界の製造業はパラダイムシフトを経験しています。


台州精振模具科技有限公司
住所:浙江省寧波市象山県城東工業園 智創智造園 25 棟 2 単元
電話:+86-574-65762018
COOKIES
当社の Web サイトでは、お客様に表示される広告をパーソナライズし、お客様が当社の Web サイトで最高のエクスペリエンスを得られるよう、Cookie および同様のテクノロジーを使用しています。 詳細については、プライバシーと Cookie ポリシーをご覧ください。
COOKIES
当社の Web サイトでは、お客様に表示される広告をパーソナライズし、お客様が当社の Web サイトで最高のエクスペリエンスを得られるよう、Cookie および同様のテクノロジーを使用しています。 詳細については、プライバシーと Cookie ポリシーをご覧ください。
これらの Cookie は、支払いなどの基本的な機能に必要です。 標準の Cookie をオフにすることはできず、お客様の情報は一切保存されません。
これらの Cookie は、カスタマー エクスペリエンスを向上させるために、サイトを使用している人の数や人気のあるページなどの情報を収集します。 これらの Cookie をオフにすると、エクスペリエンスを向上させるための情報を収集できなくなります。
これらの Cookie により、Web サイトは拡張機能とパーソナライゼーションを提供できるようになります。 これらは、当社または当社のページにサービスを追加したサードパーティプロバイダーによって設定される場合があります。 これらの Cookie を許可しない場合、これらのサービスの一部またはすべてが正しく機能しなくなる可能性があります。
これらの Cookie は、お客様が何に興味を持っているかを理解するのに役立ち、他の Web サイトで関連する広告を表示できるようになります。 これらの Cookie をオフにすると、パーソナライズされた広告を表示できなくなります。
+86-135 8680 0098 (Zhao Xia) zx@jinzeen.net
Wechatは電話番号と同じです
+86-159 5743 0850 (Ye Weizong) ywz@jinzeen.net
Wechatは電話番号と同じです
+86-158 6758 3965 (Zhou Jie) zj@jinzeen.net
Wechatは電話番号と同じです
+86-139 6836 6133 (Wang Chunying) wcy@jinzeen.net
Wechatは電話番号と同じです
+86-158 5810 0559 (Li shihui) summer@jinzeen.net
Wechat /Whatsappは電話番号と同じです
+86-198 1689 5393 (Han Ying) sales@jinzeen.net
Wechat /Whatsappは電話番号と同じです